
Design alternatives can be quickly explored and evaluated without leaving the familiar Inspire user environment. Starting from either topology optimization results or an imported CAD geometry, support structures can be easily generated and optimized. As a result, teams to cut product development and additive manufacturing costs by reducing material usage, print times and post-processing. Inspire Print3D accelerates the creation, optimization, and study of innovative, structurally efficient 3D-printed parts, providing a fast and accurate toolset for the design and process simulation of selective laser melting (SLM) parts.Įngineers can quickly understand changes to process or design that affect manufacturability, then export part and support structure geometry to major printer preparation software to produce the part. Software to be used: Altair Inspire with SimSolid set as the Solver in preferencesĮvaluation criteria: Evaluation is done based on the correctness of your simulation, prediction of von mises stress, displacement, and reaction forces.Efficient Design for Additive Manufacturing In this part of the competition, we are looking to leverage your structural simulation capability for an army shelter structure so that before deploying to the field we will be sure that the structure is going to withstand all the possible conditions.
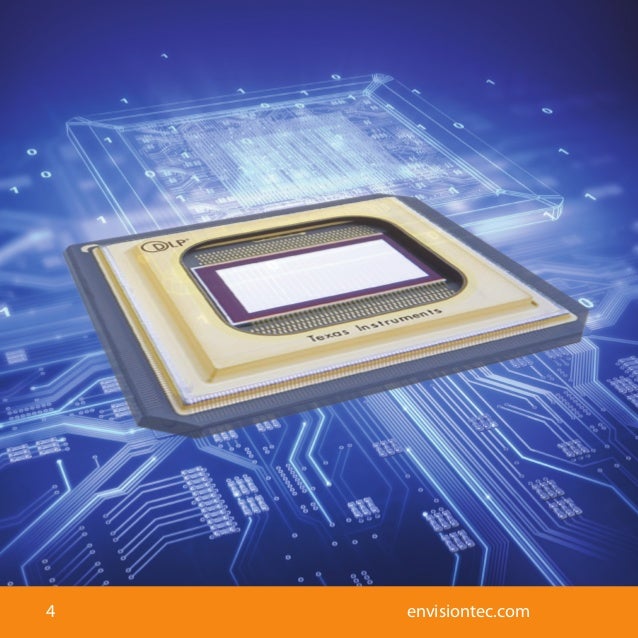

Even a small mistake like this could be costly and unacceptable for the country’s defense. It should be strong enough to sustain all the possible eventuality, be it a high wind to heavy rains to massive snowfalls.It should be light-weight as it needs to be transported long distances & deployed.
.jpg)
The structural design should fulfill three basic needs:

The current design of a shelter is to be evaluated for structural behavior to address the harsh requirements at the border posts. Problem – 1 : Rapid Structural Simulation of an Army Shelterĭescription: Defense forces are in urgent need of Army shelters for deployment at forward bases.
